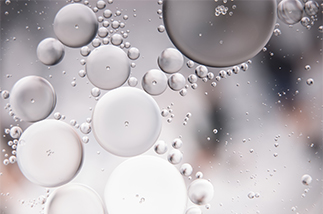
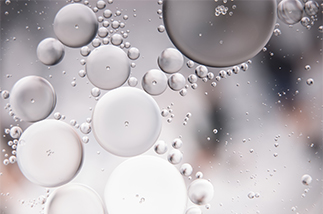
Sintered metal mesh porous material is characterized of simple structure, even mesh aperture distribution as ordinary metal woven mesh, but high strength, good integrity, stable and rigid mesh shape. Further, the material can be customized for its pore size, permeability, mechanical strength, which show excellent comprehensive performance。
FEATURES AND BENEFITS
+ Rigid, stable and even pore distribution
+ Good permeability and low resistance loss
+ Easily cleanable with smooth surface
+ High strength and workable under high differential pressure
+ Extensive materials selection
+ High temperature and corrosion resistance
+ Liable to processing and molding
+ Superior welding performance
APPLICATIONS
Petrochemical: Rectisol process (solid-liquid separation), etc.
Coal chemical: Raw oil filtration, dust collector filter, etc. Shipping industry: Ballast water treatment
Aviation industry: Hydraulic oil filtration
Metallurgical equipments: Fluidizing plate/tank
TECHNICAL SPECIFICATIONS
Materials of Construction:
Stainless steel(310S,316L, 304), Copper Alloy, Inconel、Hastelloy,FeCrAlalloy, etc.
Weldless Dimensions:
Plate max W 1000×L 1200mm
Cartridges Diameter Ф3~100mm, Length ≤1000mm
Operating Performance:
Maximum working temperature: ≤900℃
The fibers layered in metal fiber could form a 3D porous structure, providing high porosity and excellent permeability. The soft metal fiber could be pleated to significantly improve the effective filtration area in unit volume.
APPLICATIONS
Coal Chemical industry:Rectisol section
Chemical fiber and membrane industry:Filtration and the melted polymers cleaning Medicine, biological and beverage industries: Liquids clarification
General industry: Precision filtration of hydraulic and lubricating oils of machineries
TECHNICAL SPECIFICATIONS OF CARTRIDGES
Weldless Dimensions:
Diameterφ20-200mm, Length ≤1200mm
Obvious V-shaped openings will be formed in the gap between filtration pipes.
Features and Benefits
TECHNICAL SPECIFICATIONS
Pore size 15-100μm
Weldless cartridge dimension φ20-100mm L≤2000mm
APPLICATIONS
- Widely used in petrochemical and oil refining plants, as the inner and outer baskets of the radial reactors of the catalytic reforming units. In addition, such screens are often used at the inlet distributors, scaling devices, the supporting grating of catalyst bedside, and outlet collectors. They are also used in the filtration baskets of centrifugal machines, vibrating screens and many other filtration pipes. It’ s specialized in wax oil, bitumen and other high viscosity oil filtration.
- Widely used in water treatment of electric well, natural gas well, well, chemical industry, mining, paper making, environmental protection, metallurgy, foodstuff, sand control and decorative light industry.
The feature of high flux heat exchange tubes is that powder is composed on the base metal of heat exchange tubes to change the status of boiling surface to form porosity between particles and form nucleate boiling center, so as to change the mem-brane-shaped boiling into nucleate boiling and significantly improve the boiling heat transfer coefficient.
APPLICATIONS
Heat transfer of liquid-gas phase changing and boiling in the petrochemical, chemical and metallurgy industries, sea water desalination, natural gas storage and transport, air separation and refrigeration.
FEATURES AND BENEFITS
+ Double-side reinforced structure is used, such as outer longitudinal slots with inner porous or outer porous with inner slots
+ High critical heat load. The critical heat load of high flux heat exchange tube is about twice of that of ordinary tube
+ The boiling could be maintained at small temperature difference. With the same heat flow intensity, the effective temperature difference required by high flux heat exchange tubes is only 10% ~ 15% of that of ordinary smooth tubes
+ Excellent anti-blockage capacity and scaling resistance performance
TECHNICAL SPECIFICATIONS
Dimensions: Φ15~51mm; length: 1~15m
Porosity of the porous layer: 40% - 80%
Pore size of the porous layer: 30-70μm
Shear force of the porous layer: ≥150N/ mm
Total heat transfer coefficient: ≥3000 W/(m2.K)
Materials: carbon steel tubes, stainless steel tubes, copper and copper alloy tubes
To date, AEET’ s capable of manufacturing 400,000m/year high flux heat exchange tubes with excellent performance. At present, we are exploring markets and new applications and trying to provide our clients with more cost-effective products and better services.